Exploring the World of Metal Stamping: From Style to Manufacturing
Within the world of production, steel marking attracts attention as an accurate and effective technique for forming steel sheets right into numerous kinds with impressive consistency. From the initial design phase where intricate patterns materialize to the elaborate production processes, metal stamping is a blend of artistry and engineering. Delving right into this globe introduces an intricate interaction of creative thinking and technological proficiency, using a look right into a realm where development satisfies craftsmanship.
History of Metal Stamping
Steel marking, a commonly utilized manufacturing process today, has an abundant background that goes back to ancient times (Metal Stamping). The origins of metal marking can be mapped to ancient civilizations such as the Egyptians, who used marking methods to adorn precious jewelry and accessories with intricate styles. In time, metal marking advanced, with people like the Greeks and Romans utilizing it for producing coins and decorative items
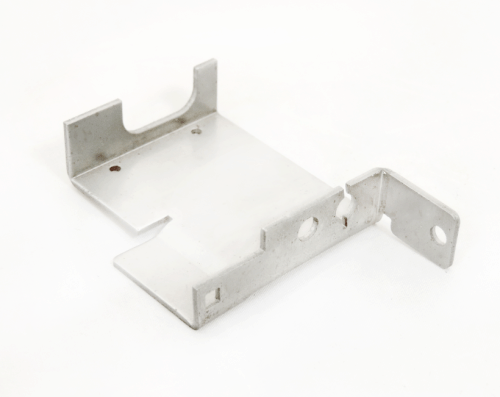
In the 20th century, steel marking continued to advance with the combination of automation and computer system numerical control (CNC) technology. These improvements even more raised the effectiveness and accuracy of metal marking processes, making it an indispensable component of modern-day manufacturing throughout industries such as auto, aerospace, and electronics. Today, steel marking stays an essential manufacturing procedure, combining custom with technology to meet the needs of a constantly developing sector.
Design Factors To Consider and Prototyping
Layout considerations in metal stamping include material selection, part geometry, tooling design, and production feasibility. Tooling design plays a considerable duty in the success of steel marking jobs, influencing component precision, device durability, and production effectiveness.
Prototyping is a critical stage in the metal marking process that permits engineers to test the layout, validate manufacturability, and make essential modifications before major production. By meticulously thinking about design aspects and making use of prototyping, producers can simplify the metal marking process and attain premium, cost-effective production end results.
Tooling and Devices Basics
Thinking about the critical function that tooling layout plays in the success of metal stamping tasks, understanding the necessary tools visit the website and devices called for is critical for attaining efficient production end results. Tooling is a fundamental element of steel marking, as it directly affects the top quality and uniformity of the final products. Crucial tools include dies, strikes, and components, which are custom-designed to shape and develop the steel right into the desired parts. Dies are the main device used to cut and develop the steel, while strikes help create holes or certain forms. Components hold the metal in position during the stamping procedure, ensuring accuracy and repeatability. Furthermore, tools such as marking presses, feeders, and coil handling systems are essential for automating the stamping process and boosting performance. Investing in premium tooling and tools not just improves production effectiveness however additionally leads to higher Related Site precision, lowered waste, and overall expense financial savings in metal stamping operations.
Manufacturing Process and Quality Assurance
Effectively managing the production procedure and implementing durable top quality control steps are crucial for guaranteeing the success of steel marking projects. The manufacturing procedure in metal stamping entails a series of steps that need to be carefully collaborated to attain optimal results.
Quality assurance in steel marking is extremely important to deliver products that meet the required specifications. Checking the stamped components at numerous phases of manufacturing aids recognize any kind of issues early on, avoiding expensive rework or scrap. Methods such as dimensional evaluation, visual evaluation, and material testing are typically employed to ensure the quality of the stamped components. By keeping rigorous top quality control criteria, makers can maintain their track record for providing premium metal stamped items.
Applications and Industry Insights
In the realm of metal stamping, the successful application of manufacturing procedures and high quality control actions straight affects the performance and integrity of various industry applications and provides important insights into the industry's operational dynamics. Additionally, metal stamping facilitates the production of numerous house devices, consisting of fridges, cleaning makers, and stoves, by offering affordable services for producing resilient and complex components. Recognizing the applications and sector understandings of steel stamping is important for optimizing production processes and boosting item high quality across various fields.
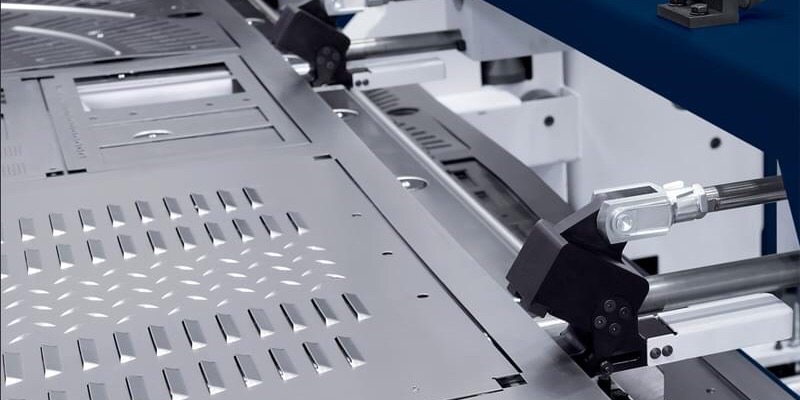
Verdict
Layout considerations, prototyping, tooling, tools, production procedures, and high quality control are essential elements of metal marking. With its widespread applications go now and market insights, metal marking continues to be a functional and efficient manufacturing procedure.
Comments on “Elevate Your Manufacturing Quality with State-of-the-Art Metal Stamping Services”